Fastest 3D printed structure in the world
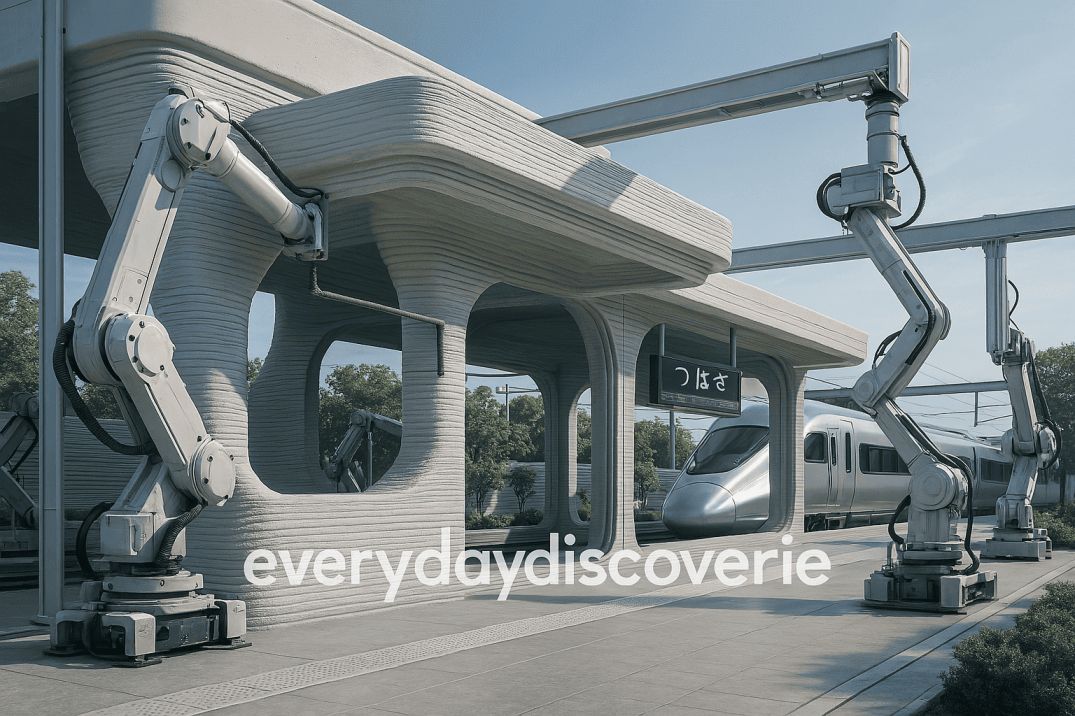
Japan Builds a 3D-Printed Train Station in Just 6 Hours: Revolutionizing Infrastructure with Innovation
In a stunning display of technology and efficiency, Japan has built a fully functional 3D-printed train station in just six hours. This groundbreaking achievement not only sets a new benchmark in modern construction but also redefines how public infrastructure projects can be designed, developed, and delivered. By integrating 3D printing in construction, Japan is leading the way toward sustainable, cost-effective, and rapid urban development.
This innovation holds the potential to transform global infrastructure, especially in the transportation sector, where timely development is crucial. Let’s dive into how this project was accomplished, why it matters, and what it means for the future.
What Is a 3D-Printed Train Station?
A 3D-printed train station is a public transportation facility constructed using additive manufacturing technology—commonly known as 3D printing. Instead of relying on conventional construction techniques that involve bricks, mortar, and extensive labor, 3D printing builds structures layer by layer using specialized materials such as concrete composites or geopolymer blends.
The station built in Japan is compact, durable, and equipped with all the essential facilities needed to function as a commuter hub, including platforms, seating areas, waiting zones, and digital displays.
How Japan Built a 3D-Printed Train Station in Just Six Hours
Using large-scale robotic arms and automated printing systems, construction engineers in Japan were able to assemble the entire structure of the station in just six hours. Here's a look at the step-by-step process:
1. Pre-Design Using CAD
Everything starts with a detailed Computer-Aided Design (CAD). The layout, dimensions, and materials were precisely planned using digital models, allowing the printer to follow exact specifications.
2. Material Preparation
A custom-made concrete mixture was used, optimized for rapid curing and high durability. This material was fed into the 3D printer.
3. Layer-by-Layer Construction
The robotic printer laid down concrete in precise layers, building the station’s walls and structural components from the ground up.f
4. Final Assembly & Tech Integration
After the core structure was printed, engineers added electrical systems, digital signage, ticketing kiosks, and smart sensors to complete the station’s functionality.
Key Features of Japan’s 3D-Printed Station
Fast Construction
The entire structure was completed in just six hours, a feat impossible using traditional construction methods.
Eco-Friendly Materials
The construction used sustainable, low-carbon concrete, reducing environmental impact and contributing to Japan's green building initiatives.
Minimal Labor Requirement
Most of the work was automated, requiring only a handful of engineers to supervise and install finishing touches.
Earthquake and Weather Resistant
Built with Japan’s seismic activity in mind, the station was designed to withstand natural disasters, ensuring long-term durability.
Smart Integration
The station includes touchless ticketing, real-time train information, solar-powered lighting, and sensor-based maintenance alerts.
Why This Innovation Matters
Solving Infrastructure Delays
Traditional station construction can take months or even years. With 3D printing, governments and agencies can rapidly deploy transportation infrastructure in a fraction of the time.
Meeting Emergency Needs
After natural disasters like earthquakes or floods, rapid reconstruction of transit systems is crucial. 3D-printed infrastructure can be a game-changer in such scenarios.
Reducing Costs
3D printing reduces material waste, labor costs, and time spent on site. The result? Significant savings for taxpayers and municipalities.
Empowering Remote Areas
Rural and remote regions often lack access to quality infrastructure. Portable 3D printers can be deployed to these locations, building customized stations on-site without the need for heavy equipment.
The Future of 3D Printing in Public Infrastructure
Japan’s successful execution of a 3D-printed train station is just the beginning. Here’s what we can expect in the future:
3D-Printed Bus Terminals & Shelters
Similar technology could be used to quickly construct bus stands, taxi depots, and bike-sharing hubs.
Custom-Designed Smart Buildings
With flexible design options, cities could use 3D printing to build aesthetically unique and functional buildings tailored to local needs.
Disaster-Relief Structures
In emergencies, pop-up hospitals, shelters, and supply centers can be printed and assembled within hours.
Sustainable Urban Planning
By reducing the carbon footprint of construction, 3D printing aligns perfectly with the goals of smart cities and sustainable development.
Conclusion: Printing the Future—One Station at a Time
Japan’s 6-hour 3D-printed train station is more than just a technological marvel—it’s a vision of what's possible when innovation meets necessity. By embracing advanced construction techniques, Japan is paving the way for faster, greener, and more inclusive infrastructure development.
As urban populations continue to rise and the demand for resilient infrastructure increases, the global construction industry must take note. The future isn’t just being built—it’s being printed, and Japan is showing us how it’s done.
Stay updated with more future-ready innovations and tech breakthroughs at Everydaydiscoverie.com